擠壓絲錐指的是采用擠壓的方法使內螺紋成形。擠壓絲錐在進入底孔后,其擠壓錐部分擠入被加工的材料之中,材料被擠向絲錐齒間的空隙處,借助材料的塑性流動性而形成螺紋的齒形。由于在加工過程中不產生切屑,擠壓絲錐亦稱為無屑絲錐(圖)。
擠壓絲錐的加工條件
1)底孔加工:在切削螺紋時,底孔直徑與螺紋內徑是一致的,也就是說,切削時底孔直徑將作為內徑保留而不被切削。在擠壓螺紋時,螺紋的內徑是通過底孔壁被擠壓絲錐的齒尖所擠壓,金屬向齒根部分方向流動而形成,故底孔的直徑要比螺紋的內徑大。如果底孔被鉆得太小,則要變形的金屬會過多地流到擠壓絲錐的螺紋谷底(內芯處),這樣形成螺紋齒太大,內徑太小,而使檢驗不合格,同時容易造成力矩增加,絲錐被折斷等危險。但如果底孔被鉆得太大,則要變形的金屬會過少,這樣形成的螺紋齒太短,內徑太大而承受力不夠。
另外值得注意的是,由于擠壓加工時材料的纖維組織未被切斷,且材料由于被擠壓而產生加工硬化,所以即使螺紋齒比切削時短50%,但其強度并不降低。所以如有可能(在保證公差精度的前提下),底孔直徑應盡量鉆得大一些(即盡量靠近上公差)。這樣,擠壓扭矩將下降而使絲錐壽命增加(圖20)。
在擠壓加工通孔螺紋時還要注意應將底孔的兩頭事先加工倒角,以便工件在進出口處不產生由于材料被擠壓而形成的鼓包。在擠壓加工盲孔螺紋時,應事先將底孔的入口端加工倒角。
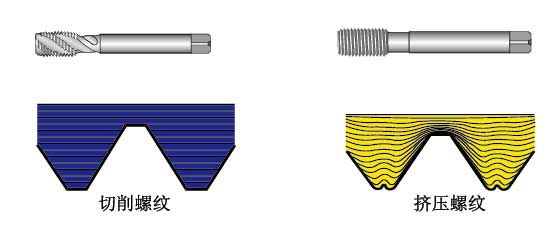
2)冷卻潤滑:潤滑在擠壓螺紋過程中取著舉足輕重的作用,能否順利地應用擠壓絲錐在很大的程度上取決于潤滑劑的特性。冷擠壓加工時的摩擦力很大,導致了單位壓力高,形成冷焊及刀瘤的危險就很大。它們可使螺紋表面質量下降,扭矩增加,絲錐壽命降低。所以為了提高擠壓絲錐的速度,獲得光潔的螺紋表面及延長工具的壽命,僅采用經表面涂層的絲錐和帶內冷是不夠的,還應采用質量相當的潤滑劑,油潤滑是最理想的。如果不得已采用乳化液,其油含量不應低于6-8%。當含油量太低時,乳化液容易燃燒,而在絲錐的齒面上形成黑斑點,絲錐壽命則大大下降。
3)擠壓速度:擠壓絲錐速度一般來說可同于螺紋切削。最常用的速度在8-15m/min之間。如果材料的延展性不佳(如鑄鋁合金),或材料的強度較高,或潤滑條件不好,則速度應降低,以獲得好的表面質量及延長絲錐壽命。
4)絲錐公差:擠壓絲錐的公差等級6HX或6GX,這是因為,首先擠壓生成的螺紋,決不比擠壓絲錐的螺紋部分更大;其次,材料被擠壓后有所收縮(擠壓螺紋后,擠壓絲錐不能再擰進,與切削絲錐不同);最后,擠壓時無誤切的危險。
上一章: 絲錐選型加工參數表
返回列表 下一章: 擠壓絲錐的優缺點及應用范圍